Juni 2017: LU Hageböke
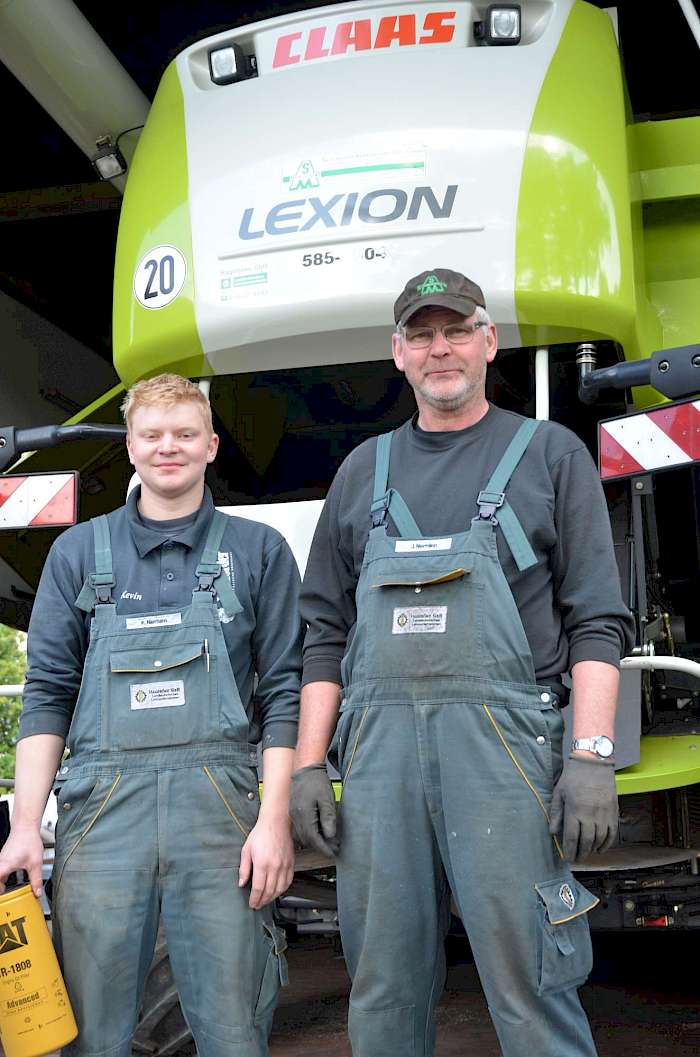
Manchmal ergeben sich Gelegenheiten, die muss man einfach ergreifen, auch wenn sie eigentlich so nicht geplant waren. So geschehen im Sommer 2014 bei Lohnunternehmer Hageböke. Über 25 Jahre hatte dort Jürgen Niermann, gelernter Landmaschinenmechaniker und im Hauptberuf in einem Metallbauunternehmen tätig, nach Feierabend sowie an Wochenenden geholfen, den Fuhrpark des Meller Lohnunternehmens in Schuss zu halten. Dann schloss sein Arbeitgeber den Betrieb mangels Nachfolger. Somit stellte sich für ihn die Herausforderung einer Neuorientierung – mit 53 Jahren nicht wirklich einfach. „Da ich sowieso darüber nachgedacht hatte, die Werkstatt anders zu organisieren, kam diese Chance, Jürgen fest einzustellen, quasi wie gerufen“, erklärt Juniorchef Hendrik Hageböke. Er hat selbst ebenfalls Landmaschinenmechaniker gelernt, ließ anschließend die Qualifikation zum Fachagrarwirt folgen und leitet seitdem mit seinem Vater die gemeinsame GmbH & Co. KG.
„Bis Sommer 2014 habe ich einen großen Teil meiner Zeit in die Werkstatt und die Instandhaltung des Fuhrparks gesteckt. Aber unser Unternehmen wächst, sodass immer mehr meiner Zeit für andere Aufgaben nötig ist. Deshalb ist es optimal, dass Jürgen seit August fest bei uns im Team ist. Und durch seine vorherige, langjährige Hilfe bei uns war er sofort im Thema drin, konnte also aus dem Stand Vollgas geben“, erläutert er und ergänzt: „Gleiches galt übrigens auch für seinen Sohn. Kevin Niermann absolviert derzeit ein Praxisjahr bei uns und macht anschließend eine Weiterbildung zum Techniker, sodass wir in der Werkstatt – rein rechnerisch nach Stunden – derzeit zwei Vollzeitkräfte haben."
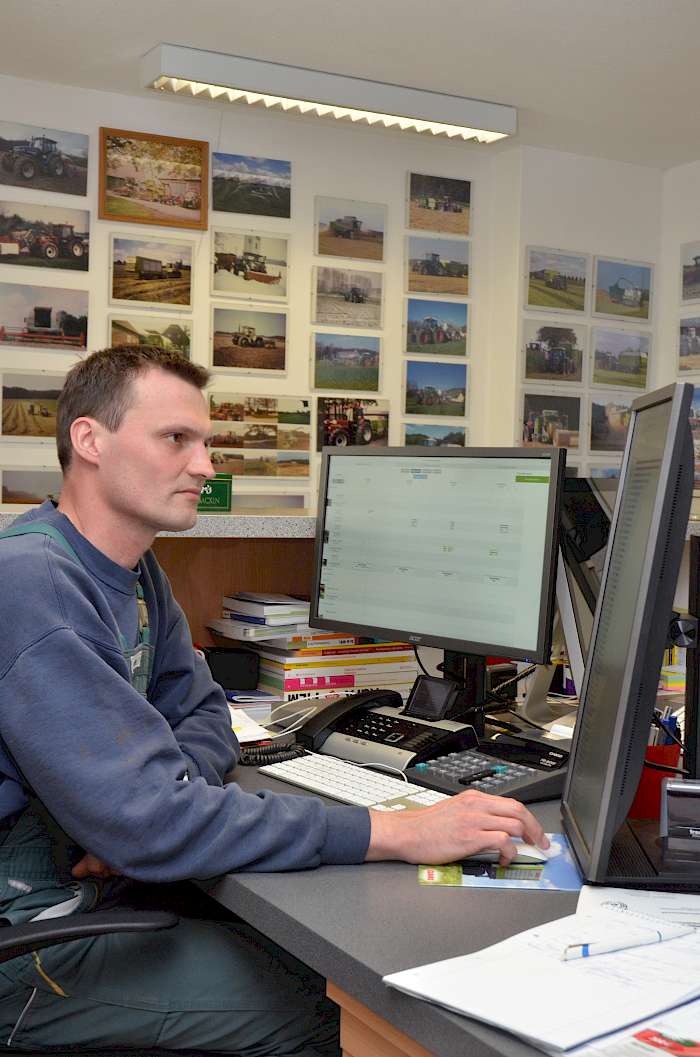
Raus aus dem Blindflug
Aber wo liegt eigentlich dieser „Balancepunkt“? Eine Frage, die nicht pauschal mit einer Zahl zu beantworten ist, wie der Lohnunternehmer betont. Vor allem ist es seines Erachtens dazu enorm wichtig, die tatsächlichen Kosten so exakt wie möglich zu kennen. Bis 2013 basierte dieses Wissen auf relativ zeitaufwendigen Auswertungen von Rechnungen, Stundenzetteln und Exceltabellen. Daraus ließ sich bereits viel ableiten – aber vielfach eben doch manchmal mehr geschätzt als wirklich gewusst, wie er unumwunden zugibt, was bei Lichte betrachtet einem Blindflug gleichkomme. Deshalb fassten Hendrik Hageböke und sein Vater den Entschluss, in Betriebsmanagementsoftware zu investieren. Die Wahl fiel auf Agrarmonitor von betriko, und seit Anfang 2014 ist das Programm in Melle scharf geschaltet. „Grundsätzliche Tendenzen der Kennzahlen lassen sich nach 18 Monaten noch nicht ableiten, da wir dazu mindestens zwei, besser drei komplette Jahre als Daten verfügbar haben sollten. Aber schon jetzt haben wir diverse Erkenntnisse daraus ziehen können, die uns überrascht haben. Das gilt auch für die Werkstatt“, meint der Lohnunternehmer.
Zu den wichtigsten Voraussetzungen neben Hard- und Software gehört für ihn die möglichst exakte Zuordnung der Arbeitszeiten – wozu sicher die Nutzung der iPads positiv beigetragen habe. Der Erfolg dessen sei natürlich abhängig von der Konsequenz und Disziplin aller Mitarbeiter, was die Erfassung betrifft. Aber diesbezüglich verdiene das gesamte Team gute Noten, wie er ergänzt: „Wichtig war mir aber auch, meine Vorgaben dazu, was wann zu erfassen ist, praxistauglich zu gestalten. Klar, die Stunden müssen lückenlos über den Tag hinweg verbucht sein, besonders bei Kundenaufträgen, die ja berechnet werden. Ob allerdings bei kleineren internen Tätigkeiten nun 5 min unter dem Stichwort Hof oder unter Werkstatt verbucht werden, macht aus meiner Sicht den Kohl nicht fett. Die Zeiterfassung muss praktikabel bleiben und die Zuordnung in der Grundrichtung passen, vor allem aber nicht in zeitraubende Erbsenzählerei ausarten“, ist der Lohnunternehmer überzeugt.
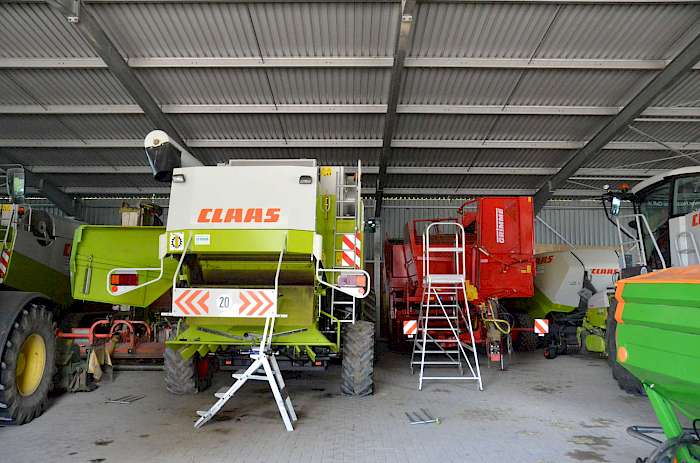
Wissen macht Ah!
Obwohl erst seit knapp 18 Monaten im Einsatz, hat Agrarmonitor bereits diverse interessante Erkenntnisse gebracht, wie Hendrik Hageböke erklärt. Dazu gehört die Stundenverteilung für „Werkstatt & Hof“. So beliefen sich die Reparaturen an Maschinen 2014 auf gut 1.900 h – mehr, als in der alten Papiererfassung registriert. Erhellend war für ihn auch die Erkenntnis aus dem Jahr 2014, dass rund 200 h für die Ersatzteilbeschaffung und 770 h für die Werkstatt-Organisation verwendet wurden. Zu letztgenanntem gehören in seiner Definition neben der Arbeitseinteilung und Vorbereitung von Arbeiten auch Fahrten zu Landmaschinenhändlern oder der Bau von Vorrichtungen für die Werkstatt.
Auf Maschinenwartung entfielen demzufolge etwa 440 h, auf das Reinigen und Waschen von Technik insgesamt 660 h. Allein das Schleifen von Messer fiel mit sage und schreibe 92 h zu Buche. „Besonders bei Wartung und Reinigung sind natürlich nicht nur unsere zwei Werkstattspezialisten, sondern auch die anderen Fahrer gefordert. Diese Zeiten werden jetzt auch exakt zur jeweiligen Maschine verbucht“, so Hendrik Hageböke.
Als echten Hammer empfindet er die rund 650 h Rüstzeiten, was deutlich mehr ist, als er erwartet hätte. „Bei Lichte betrachtet, ist dies aber logisch und völlig ok. Wir haben einen relativ knapp bemessenen Maschinenbestand, sodass bei vielen unterschiedlichen Kundenaufträgen häufiger die Traktoren umgehängt oder Maschinen umgerüstet werden müssen. Außerdem vermieten wir auch Güllefässer und einige andere Geräte an Landwirte, sodass hier der Vor- und Nachbereitungsaufwand größer als sonst ist. Jetzt können wir Zeiten und Kosten viel besser zuordnen – und auch in die Preiskalkulation einfließen lassen.“
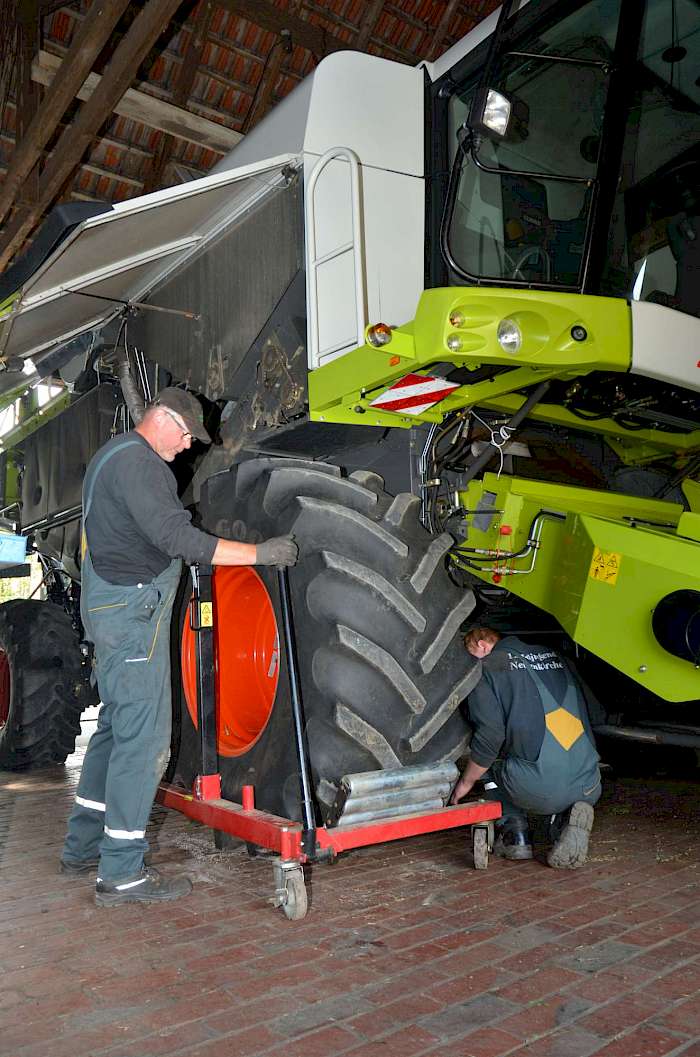
Fachhandel bleibt wichtig
Das Stichwort Preis bringt ihn auch noch auf einen anderen Aspekt: die Analyse der Maschinengesamtkosten. Denn Reparaturanfälligkeit, Werkstatt-Fremdrechnungen und Ersatzteilkosten schlagen sich teilweise in erschreckend hohem Maß nieder, so seine Einschätzung. „Dieses Wissen benötige ich aber nicht nur zur Kalkulation unserer Arbeitspreise, sondern genauso als Entscheidungshilfe bei Investitionen. Und da kommt so manches Fabrikat oder Modell gar nicht so gut weg, wie man es gefühlt vermuten würde“, betont Hendrik Hageböke schmunzelnd.
Nicht von der Hand zu weisen sind in dem Zusammenhang allerdings die eigenen Werkstattkosten. Sie fallen im Meller Lohnunternehmen nicht unter die sprichwörtlichen „Eh-da-Kosten“, sondern werden ebenso akribisch kalkuliert. Hierzu werden die auf die Werkstatt gebuchten Stunden mit den jeweiligen Mitarbeiter-Lohnsätzen bewertet – worin auch alle Lohnnebenkosten enthalten sind. Werkstattausrüstung, Fortbildung und andere Kosten fallen unter die Allgemeinkosten, die nach festem Schlüssel umgelegt werden.
Doch wäre es unter dem Strich nicht günstiger, stärker die externen Fachwerkstätten einzubeziehen, statt selbst in Ausrüstung, Weiterbildung und Personal zu investieren? Hier müsse durchaus differenziert geurteilt werden, so seine Überzeugung: „Für unser Unternehmen stehen neben der Qualität der Arbeit vor allem Schnelligkeit und größtmögliche Einsatzflexibilität ganz vorn in der Prioritätenliste. Das geht nur, wenn wir den Maschinenpark im Wesentlichen selbst betreuen und auch Reparaturen zeitnah selbst durchführen können. Deshalb ist der Ausbau der Werkstatt für mich gesetzt, denn sie sichert uns sozusagen die Grundlast in der Einsatzsicherheit der Maschinen. Natürlich wachsen diese Kosten spürbar, doch das ist in Relation zum Wachstum des Unternehmens angemessen – und immer noch günstiger als die externen Kosten, die sonst anfallen würden. Definitiv ist es aber nicht unser Ziel, die Arbeit der Fachwerkstätten komplett selbst zu erledigen. Das wäre uns aufgrund von Qualifikation und Ausrüstung fachlich und finanziell auch gar nicht möglich, selbst, wenn wir es wollten.“
Die Zusammenarbeit mit den benachbarten Händlern LVD Krone und Agravis Saltenbrock, ist und bleibt für ihn wichtig, zumal er das Verhältnis zu beiden als gut bezeichnet. Die tägliche Wartung, Maschinenreinigung und Nach- bzw. Vorsaisonchecks macht das Hageböke-Team selbst. Gleiches gilt für die regulären Inspektionen, ausgenommen diejenigen bei 100 h und bei 1.000 h. Austausch von Verschleißteilen, mechanische Reparaturen und teils Hydraulikarbeiten stehen wieder auf der eigenen To-do-Liste. „Wenn es allerdings um elektronische Diagnosen, Reparaturen am Antriebsstrang oder um Elektrik bzw. Elektronik geht, holen wir gern die externen Experten dazu“, so der Lohnunternehmer.
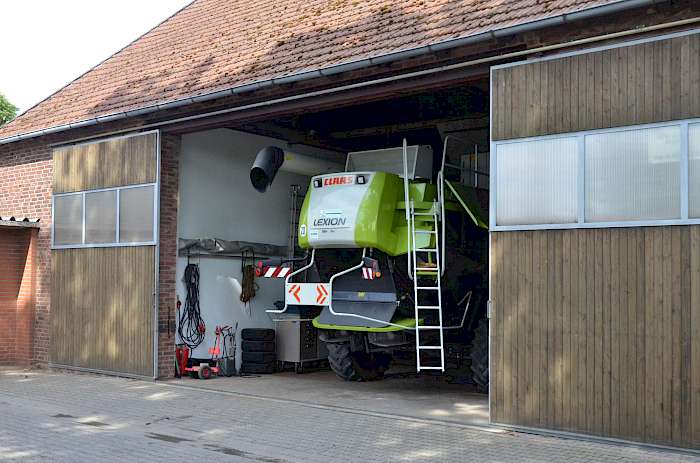
Bauliche Erweiterung geplant
Die eigene Werkstatt ist bei LU Hageböke also essenziell und wird weiter an Bedeutung gewinnen. Personell sieht sich der Unternehmer inzwischen sehr gut aufgestellt. Eine Investition wird mittelfristig jedoch nicht vermeidbar sein: die Erweiterung der Werkstatt. Bisher hat sie ihren Platz in einer Fachwerkscheune des ehemaligen Hofgrundstücks. Stehen ein Häcksler und ein Mähdrescher zugleich zum Check darin, wird es schon arg eng. Einige Arbeiten erfolgen deshalb bei Bedarf in der vor einigen Jahren neu errichteten Maschinenhalle nebenan. Aber erstens ist die ebenfalls schon zu klein, und zweitens ist es ihm außerdem wichtig, auch das Arbeitsumfeld der Werkstatt zeitgemäß zu gestalten.
„Platz ist auf unserem Grundstück an sich nicht der begrenzende Faktor. Aber die Genehmigungsverfahren für Neubauten sind schon eine Hürde. Noch steht nicht fest, ob wir die Scheune abreißen und komplett neu bauen, oder ob wir das bisherige Gebäude um einen neuen Teil erweitern. Ideen dazu habe ich schon einige – aber noch ist nichts beschlossen. Es hat ja keine große Eile. Doch dass etwas passieren muss, steht für mich fest“, meint Hendrik Hageböke abschließend.
[...]
Jens Noordhof, Redaktion LOHNUNTERNEHMEN
Den vollständigen Bericht lesen Sie in der Zeitschrift LOHNUNTERNEHMEN Ausgabe Juli 2015.