Januar 2017: LU Huber
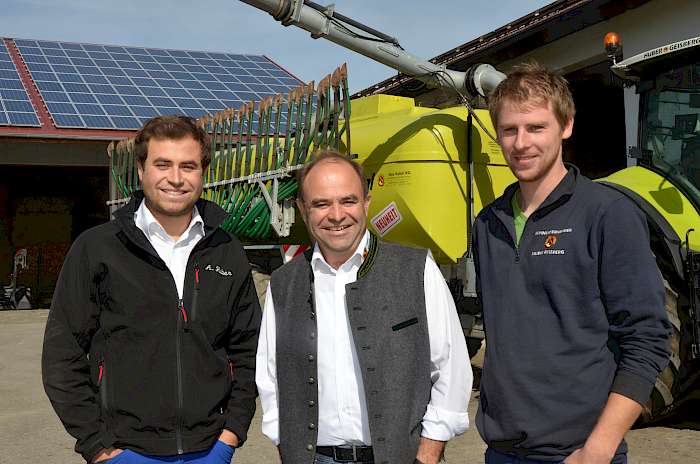
Das Runde muss ins Eckige – diese Aussage ist jedem Fußballfan bekannt. Übertragen auf das Thema Gülle, könnte man den Spruch ändern in „das Feste muss raus aus dem Flüssigen“. „Müssen“ ist dabei etwas vehement formuliert, denn im Optimalfall kann eine gut homogenisierte Gülle nährstoffschonend auf Feld oder Wiese ausgebracht werden. Aber die Verhältnisse sind in der Praxis oft eben nicht optimal. Und vor dem Hintergrund der sich abzeichnenden, schärferen Auflagen der Düngeverordnung wird die Zahl der Überschussgebiete, also auch die Notwendigkeit zu längeren Transportwegen, zunehmen. Um dabei nicht nur „überflüssiges“ Wasser durch die Republik zu schaukeln, arbeiten diverse Hersteller zur Verbesserung der Transportwürdigkeit seit längerem an geeigneten Techniklösungen zur Separation von Feststoffen aus Gülle.
Doch nicht nur der Aspekt der Transportkosten spielt dabei eine Rolle, wie Alfons Huber sen., Lohnunternehmer aus dem oberbayerischen Halsbach, betont: „In unserer Region finden sich Milchviehbetriebe, aber ebenso Schweinehalter und Biogasanlagen – mit jeweils sehr unterschiedlicher Gülle. Hier würde die Separation durchaus mehrere positive Effekte haben.“ So ergebe sich speziell bei Milchviehbetrieben mit Laufställen häufiger das Problem eines relativ hohen Strohanteils in der Gülle, mit der Folge größerer Verstopfungsgefahr bei der Ausbringung.
Ähnlich problematisch gestalte sich zu dickflüssige Gülle oder Gärrestsubstrat, wie es etwa bei Biogasanlagen zu finden sei. „Besonders in trockenen Jahren kann dies bei Ausbringung mit Schleppschlauch auf Grünland zu einem Problem werden, weil sich Reste davon später noch im Futter wiederfinden. Indem wir mittels Separation einen Teil der Festmasse aus der Gülle herausholen und die Flüssigkeit wieder in den Behälter zurückpumpen, verbessern wir die Rührfähigkeit und damit die anschließende Ausbringung“, erklärt er.
Sein Sohn ergänzt noch einen weiteren Aspekt: die begrenzten Lagerkapazitäten in vielen Betrieben. „Durch die Trennung von festen und flüssigen Bestandteilen würden wir die Kapazität der Güllebehälter erweitern, denn die Feststoffe können an anderer Stelle gelagert werden. Oder sie werden umgehend genutzt, zum Beispiel als Einstreu. Und die feste Phase aus Gülle taugt nach unserer Erfahrung recht gut als Substrat in der Biogasanlage.“
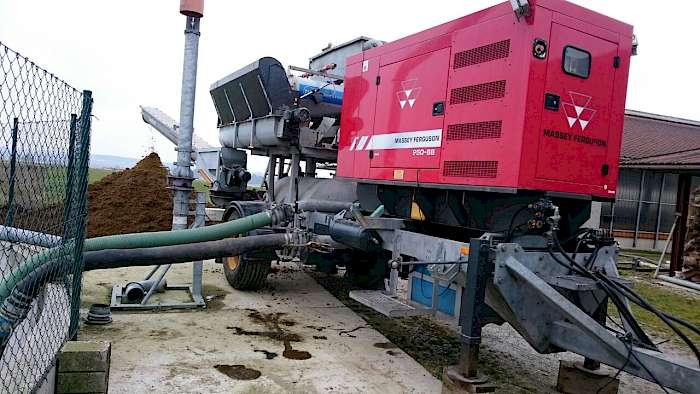
Testlauf ab Januar
Wer jedoch Vater und Sohn Huber kennt, weiß um ihre Tatkraft und Entschlussfreudigkeit, nach dem Motto: Grau ist alle Theorie, viel besser ist, es auszuprobieren. Gesagt, getan. 2014 machten sich beide auf die Suche nach passender Separationstechnik. Zweifelsfrei für beide war, eine mobile Anlage zu testen, um damit direkt bei ihren Kunden, rund 60 Viehhaltern und 30 Biogasanlagen, vor Ort arbeiten zu können. Der erste Versuch, eine kompakte Anlage auf einem Pkw-Anhänger mit Tandemachse, erwies sich umgehend als Flopp. „Die Leistung passte nicht und die Technik war nicht robust genug. Außerdem ist das Risiko zu groß, dass sich die Landwirte einen Separator dieser Größe gleich selbst kaufen. Für uns als Dienstleister musste also eine größere Lösung her“, so der Junior.
Aus verschiedenen weiteren Beispielen kristallisierte sich dann jedoch rasch eine mobile Anlage des niederländischen Herstellers Slootsmid heraus. Den Tipp dazu bekamen die Hubers von einem hessischen Kollegen. Da es sich erst um eine Testphase handeln sollte, entschieden sich die beiden Lohnunternehmer dazu, das Gerät nicht gleich zu kaufen, sondern erst einmal zu mieten. Schließlich fiel die Wahl auf den gezogenen Typ SMS 1-4 mit drei Separatoren (maximal vier wären möglich) und aufgebautem Motorenaggregat. Letzteres erlaubt die volle Leistungszufuhr unabhängig vom Traktor“, berichtet Alfons Huber sen.
Im Januar 2015 startete schließlich in Halsbach die auf drei Monate angelegte Testphase. Die Handhabung der Technik bezeichnen die Hubers als gut und praxistauglich. Auch die Leistung mit 40 bis 50 m3/h sei in Ordnung, wobei hier der Zustand der Gülle schon deutlichen Einfluss habe. Biogasrestsubstrat erwies sich als die am effektivsten trennbare Masse, so die Erfahrung. Einfluss auf den Stundendurchsatz habe natürlich auch der gewünschte Trockensubstanzgehalt der separierten Feststoffe, den man an der Maschine einstellen könne. Unabdingbar war und ist für beide, mit Blick auf das schon erwähnte Strohproblem, auf jeden Fall ein vorgeschalteter Zerkleinerer. „Insgesamt konnten wir in den drei Testmonaten im Schnitt aller Kundenbetriebe das Volumen der Gülle um gut 20 % reduzieren, in der Spitze sogar um über 30 %“, fügt Huber jun. hinzu.
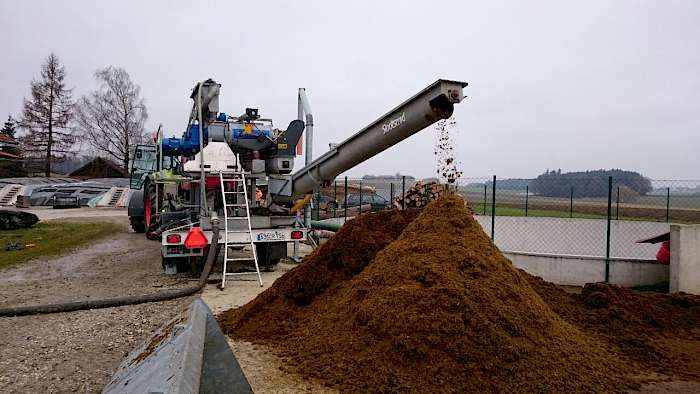
Warten auf die „DVO“
Von Januar bis April „verarbeiteten“ die Halsbacher Dienstleister im ersten Quartal 2015 rund 8.000 m3 Gülle mit dem Gerät. Angesichts von rund 100.000 m3, die im Schnitt der Jahre von Huber ausgebracht werden, war dies also durchaus eine aussagekräftige Testmenge. Der größte Teil der flüssigen Phase musste zwischengelagert werden. Somit sei ein entsprechender zweiter Güllebehälter ratsam. Dafür eigene sich aber durchaus ebenso eine klassische Jauchegrube, wie sie in vielen Betrieben noch vorhanden sei, so der Seniorchef. „Natürlich kann die Flüssigkeit auch gleich direkt in ein Güllefass gepumpt werden. Aber das wäre aus unserer Sicht nur sinnvoll, wenn der Landwirt sein eigenes Fass danebenstellt, wir also einzig die Dienstleistung des Separierens erbringen. Wenn wir auch transportieren und ausbringen sollen, reicht die Schlagkraft für eine effiziente Logistik ohne Zwischenpuffer nicht“, so seine Feststellung.
Im Großen und Ganzen fällt das Fazit der beiden Profis auch mit etwas zeitlicher Distanz unverändert positiv aus. Trotzdem gab es noch keine Entscheidung für den Kauf der mobilen Anlage. „Bevor die Novelle der Düngeverordnung nicht endgültig beschlossen ist, machen so umfangreiche Investitionen mit mehr als 150.000 € aus unserer Sicht keinen Sinn“, betont der Seniorchef.
Rentabel wäre die Technik aus seiner Sicht allemal. In besagter Probephase berechnete der Lohnunternehmer den Landwirten 2 €/m3 Gülle für das Separieren. „Eigentlich müssten es 2,50 bis 3 € sein, aber zumindest derzeit ist dies hier in der Region nicht durchsetzbar. Wenn ich mir etwas wünschen dürfte, wäre für eine bessere Wirtschaftlichkeit eine Durchsatzleistung einer solchen Anlage auf etwa 60 m3/h zu steigern. Doch das sollte nach meiner Einschätzung kein Problem sein“, meint Alfons jun. zuversichtlich.
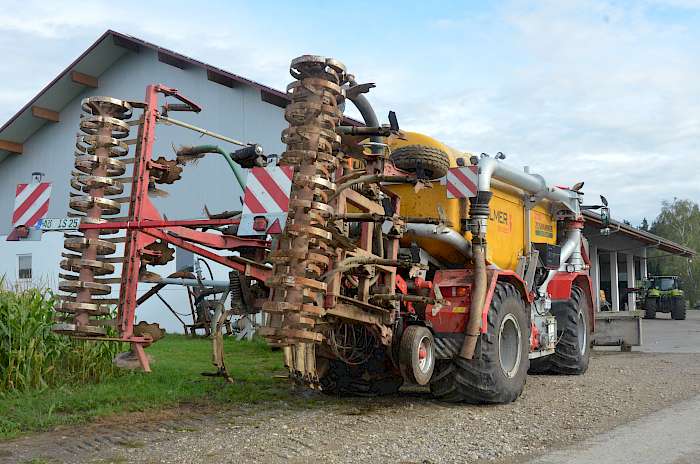
Gülle aufs Grünland
Neben den betriebswirtschaftlichen Aspekten und den politischen Rahmenbedingungen fällt beim Abwägen des Pro und Kontra der Gülleseparation aber noch ein weiterer Punkt in die Waagschale, wie Alfons sen. hervorhebt: die Ausbringtechnik. Bisher werden nach seiner Darstellung in seiner Region deutlich mehr als 90 % der Gülle auf Ackerflächen ausgebracht und nicht auf Grünland. Zweitens arbeiten viele Landwirte noch mit Pralltellern. „Beides wird sich mit der Novelle der neuen Düngeverordnung meines Erachtens rasch ändern, sodass das Grünland in Sachen Gülle massiv in den Mittelpunkt rückt.“
Die Frage ist für ihn dann aber, welche Technik dafür am besten geeignet ist und was die Landwirte akzeptieren. Gezogene Tandem- und Tridemfässer sind aufgrund der befürchteten Grasnarbenschäden bisher ein „No-Go“ für die Kunden. Ergo kommt bei Huber entweder der Holmer-Selbstfahrer zum Einsatz, mit dem bisher schon etwa die Hälfte der Acker-Gülle ausgebracht wird. Oder ein das Einachs-Güllefass ist die Technik der Wahl, was allerdings die Schlagkraft deutlich begrenzt, wie Huber jun. betont. Eine Lösung sehen Vater und Sohn in einem Tandemfass mit einer Teleskopachse und 18-m³-Fass, das im kommenden Frühjahr testweise rund um Halsbach speziell auf Grünland laufen soll. „Dann werden wir auch probieren, unseren Kunden die Vorteile des Schlitzens auf Grünland näherzubringen. Bisher gibt es bei ihnen dafür wenig Begeisterung. Aber wenn die Separierung startet, erübrigt sich die Sorge um verschmutztes Futter. Doch zuerst ist erst mal die Politik am Zug, für klare Verhältnisse und eine verlässliche Perspektive zu sorgen. Dann werden wir weiter investieren – die Erfahrungen haben wir ja bereits“, erklärt der Seniorchef abschließend.
Jens Noordhof, Redaktion LOHNUNTERNEHMEN
Der Artikel ist in der Zeitschrift LOHNUNTERNEHMEN Ausgabe Januar 2016 erschienen.